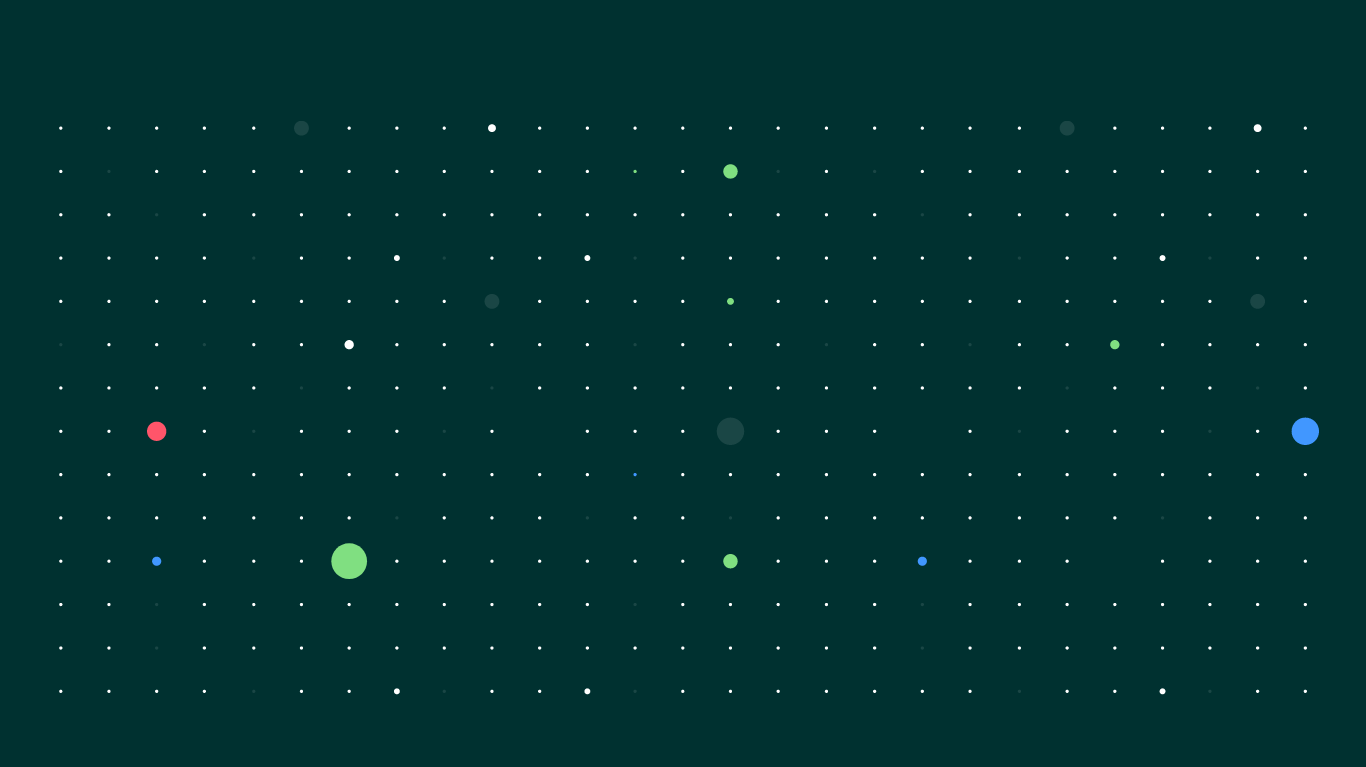
Lessons Learned: Why Projects Succeed with Interface Management
In the project world, as in life, some of the most important lessons come from looking at past failures. It is a long-acknowledged problem that large, complex, modular-based projects struggle to achieve on-time, on-budget project performance. This is largely due to mismanaged interface dependencies.
When interface management doesn’t get appropriate attention, things will go wrong, projects will be delayed and costs will increase. For interface management to be successful, project executives must revisit lessons from past projects to fully understand why interface management is essential to project success. This article examines a failed project and illustrates how proper interface management could have helped the project succeed.
Failed Project Background Information
This study examines the installation and delivery of an offshore oil project that was delayed by more than one year due to non-conformity issues associated with 3 gas turbine power generation (GTG) packages. These GTG packages were designed to be installed in the top deck of the platform at the fabrication yard before the topside module barge sea fastening and load out could occur.
Investigation into this project’s issues revealed there was significant confusion with the GTG scope requirements between the package supplier, the EPC contractor and, the client (company). The overall project scope for the EPC contractor was limited to the engineering and provisioning of procurement documentation of the GTGs and did not include the purchase of the GTGs. The client was responsible for the purchase. The 3 GTG packages were provided by the client to the EPC contractor as free issued items and were to be installed on the top deck of the offshore platform at their fabrication yard.
The GTGs were designed to run on diesel or gas. Diesel fuel was to be available if needed for a black start, as well as any time the gas pressure may not be sufficient to run the gas turbine. The expected back pressure of the diesel fuel in the intersection (i.e. tie-in point) of the GTG was 1.2 Bar and the system required a minimum of one full day’s worth of diesel to be available in the GTG day tank.
In the original design, the GTG day tank was expected to be located at an elevation of 15 meters above the platform top deck with the supply pipe to be run to the GTG tie-in point. By this design, the liquid fuel would be provided at the tie-in point of the GTG at a pressure greater than the pressure provided by gravity.
During the early stages of the detail design, the EPC contractor realized the structure planned to support the big day tank did not comply with the overall structural safety design of the platform. To accommodate this safety compliance issue, the EPC proposed relocating the day tank into the same level of the top deck where the GTGs were located, as opposed to the original design of 15 meters above, and convinced the client to approve this change. By this new design, a booster pump system would be needed to provide the required pressure of the liquid fuel the GTG would need to operate.
The newly required booster pump, however, was not properly reflected within the scope supply of the GTGs used in the bidding documents for purchasing these items. As such, the package supplier was not requested to add the booster pumps within the original scope. Even within the late stages of package delivery, none of the parties realized they had overlooked the new system requirements needed to ensure adequate liquid fuel pressure would be available to power the GTGs. With so many parties involved and such complex and heavily integrated designs, this type of interface issue can, and often does, occur with significant cost and schedule delays.
As a result of this interface issue with the GTG packages, a great deal of finger pointing and conflict between the 3 project parties occurred. Several months of negotiating were spent to figure out who was responsible for the mismatch and ultimately, who was going to pay for the associated costs. The client believed the EPC contractors were at fault for not reflecting the proper changes within the PO documents. The EPC contractor felt the client had been informed and had approved the change, and should have checked the PO documents to ensure the requirements were met and the package supplier was aware of the change. The supplier, working based on the original design, believed their scope did not include the supply of the booster pumps.
Accounting for the change at such a late stage in production ended up being very costly for the client and, of course, was not considered in the original project budget. The three booster pump kits were very expensive and the overall changes required much rework to meet the new requirements.
The problem was eventually resolved, but the resulting process caused additional issues further down the project schedule that further jeopardized the project and delayed start-up.
- The additional impact included:
- Significant additional costs for the new fuel supply system.
- Additional time and resources to determine the problem’s root cause and solution.
- Considerable time and resources required to reschedule the project.
- Considerable changes to the launching plan due to timing of the new platform completion date (e.g. vessels, crane barges, and marine aids were not available at platform completion and scheduling of these resources needed to occur during favourable seasonal conditions and cyclone-free periods necessary for offshore installation).
- Additional cost and schedule time to rework and redesign the affected area and systems within the platform.
- Additional cost for the project management team engagement due to extended period for project delivery.
Interface Management Improves Project Success
Looking at the root cause of this failed project, it is certain that an appropriate interface management process would have avoided all of these issues. With a properly implemented and executed interface management procedure, the mismatch of parts would have been avoided, in turn avoiding the subsequent delay on the project’s delivery and the additional rework required.
One of the key lessons learned from this is when interface management is implemented, the likelihood of project success increases dramatically for the following reasons:
- The effect of the interface changes would be recorded and reflected in the project plan.
- The design change would trigger a scope review by the interface management team to ensure all details of the changes are identified and all stakeholders are properly notified.
- The project integrity would be reviewed by all parties due to new changes identified by interface management team coordination.
- The interface management team would review all scope limits of all parties and all parties would be informed of the revision in their scope limit and interface supply.
- All parties would communicate to ensure everyone understands the requirements and limits of each party’s scope, including their own.
- Regular interface meeting progress reviews would be planned and managed by the interface management team.
- The project schedule would be linked to the interface management plan and appropriately updated if there is a new change on interface delivery milestones.
- The EPC contractor’s offshore logistics plan would be revised and updated to reflect the change of installation period and the booking dates of the vessels, barges, cranes and installation aides would be updated accordingly.
Overall, the project’s final cost, schedule, and plan could have been properly managed if the progress and integrity of project interfaces were monitored and coordinated by the project interface management team.
Setting up a proper interface management process with appropriate tools and systems will include additional upfront costs and resources, but can potentially save in the excess of tens or hundreds of millions of dollars by avoiding rework, delays, and subsequent production loss. For more information and to join the conversation visit the LinkedIn Interface Management group at: http://bit.ly/InterfaceManagementLIGroup